How Does the Structure of Mixer Influence the Cost of Concrete Mixer with Pump?
In today's competitive construction machinery market, choosing a concrete mixer with pump has become a preferred solution for many contractors and builders aiming for efficiency, convenience, and cost control. However, one frequently asked question is: *What drives the concrete pump cost, and how does the structure of the mixer factor into it?* The answer lies in understanding how the design, components, and build quality of the mixer can significantly affect both upfront investment and long-term expenses.
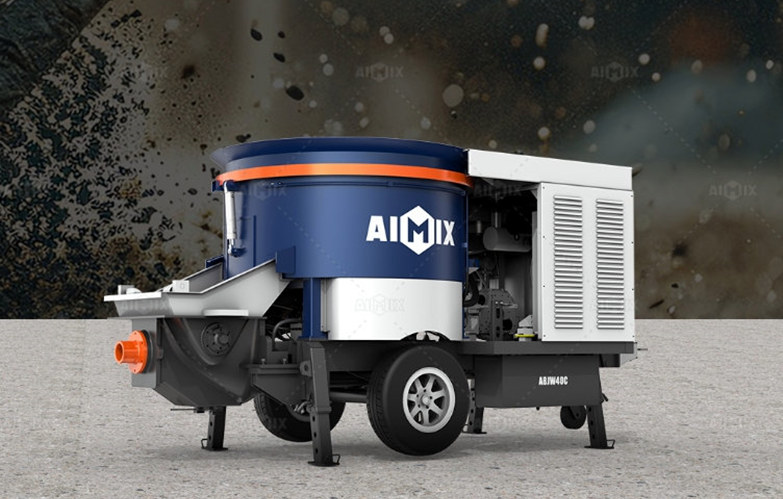
Overview: Concrete Mixer with Pump
A concrete mixer with pump combines two functions—mixing concrete and pumping it to designated locations—into a single machine. It eliminates the need for a separate mixer and pump unit, making it ideal for small to medium construction sites, especially where space is limited or mobility is crucial. These machines can be powered by diesel or electricity, and they come in various capacities to suit different project requirements.
While the dual-functionality saves time and labor, the overall concrete pump cost is directly affected by the structural design of the mixer component. Let's explore the core elements of the mixer that influence the price point.
Mixer Drum Size and Capacity
The size of the mixer drum is one of the most visible and impactful structural components influencing the cost. Larger drums allow for higher mixing volumes, increasing worksite efficiency but also raising material and manufacturing costs.
Small-capacity mixers (20–30 m³/h) are more affordable and suitable for minor residential or rural projects.
Larger mixers (40–60 m³/h), designed for commercial or infrastructure work, are structurally reinforced and come with a higher price tag.
Thus, choosing a mixer with an appropriate drum size based on actual project needs can help avoid unnecessary spending.
Mixing System Type: Twin Shaft vs. Drum Mixer
The mixing mechanism significantly influences both performance and cost:
Twin shaft mixers offer high-intensity, rapid mixing and are ideal for heavy-duty use. Their structure involves dual shafts with paddles and a more complex housing, leading to higher concrete pump cost.
Drum-type mixers, often used in mobile units, are simpler, lighter, and more cost-effective but may offer less homogeneity in the mix.
Contractors aiming for industrial-grade strength and faster mixing cycles may opt for twin-shaft systems despite their higher price due to the long-term efficiency gains.
Material of Construction
The materials used in the mixer's structure—especially the drum and internal paddles—directly affect durability, wear resistance, and overall cost.
- Mixers made with wear-resistant alloy steel last longer, withstand abrasive materials like gravel or coarse sand, and reduce maintenance needs.
- Lower-cost models may use mild steel or lower-grade metals, which reduce the initial concrete pump cost but result in more frequent repairs and replacements.
Long-term thinking favors investing in high-grade structural materials for better performance and reduced downtime.
Agitation System and Lining
Some advanced mixers come with replaceable liners or agitation paddles made of high-manganese steel or carbide alloys. While these enhancements boost the machine's efficiency and reduce sticking or clogging, they increase production cost and, consequently, the retail price.
The presence of a robust vibration and mixing system is vital for projects requiring consistent concrete quality, particularly in commercial or public infrastructure.
Structural Reinforcement for Stability
In a concrete mixer with pump, the mixer must be structurally integrated with the pumping system. This requires a reinforced chassis and mounting system to ensure machine stability during mixing and pumping.
Heavier-duty reinforcement translates to better operational safety but also adds to the machine's weight and cost. Some manufacturers use I-beam or rectangular hollow-section frames, which are structurally sound but more expensive to produce.
For buyers working on uneven or rugged terrain, these reinforced designs provide better safety and reduce wear—but increase initial investment.
Integration With the Pumping System
The seamless integration between mixer and pump—especially how the hopper feeds into the pump cylinder—also affects the overall cost. Machines with better integration often feature:
Automated feeding systems
Hydraulic-driven hopper mixing paddles
Sensors to regulate concrete flow
Such smart designs reduce labor requirements and improve output, but they also add complexity and expense to the unit. A basic setup may suffice for a rural project, but large-scale urban construction may demand these integrated structures for efficiency.
Portability Features
Structural features that support portability—such as wheels, tow bars, or skids—also impact cost. A mixer with off-road tires and a shock-absorbent base structure will be more expensive than a stationary unit with simple footings.
Portability is especially important in regions with poor infrastructure or in countries like Australia, the Philippines, or India, where job sites are often remote.
Manufacturing and Assembly Precision
Finally, the precision of structural assembly also affects pricing. Mixers with tight tolerances, smooth welds, and balanced load distribution cost more due to superior engineering. These high-precision structures improve safety, reduce wear and tear, and ensure consistent mixing over time.
Low-cost models might cut corners in welding quality or joint reinforcements, which could lead to premature structural failures or alignment issues.
The structure of a mixer in a concrete mixer with pump is not merely about shape or size—it reflects the machine's capability, durability, and efficiency. Each structural element—from drum size and materials to frame reinforcement and mixing system type—has a direct impact on the concrete pump cost.
Understanding these details helps buyers make more informed decisions. Instead of focusing solely on the sticker price, evaluating the structure for long-term reliability and performance often leads to a better return on investment.
Contractors should ask suppliers for detailed specs, inspect structural designs, and request performance data before purchase. A slightly higher upfront cost for a well-structured mixer can mean significantly lower maintenance costs, fewer delays, and better concrete quality over the long haul.
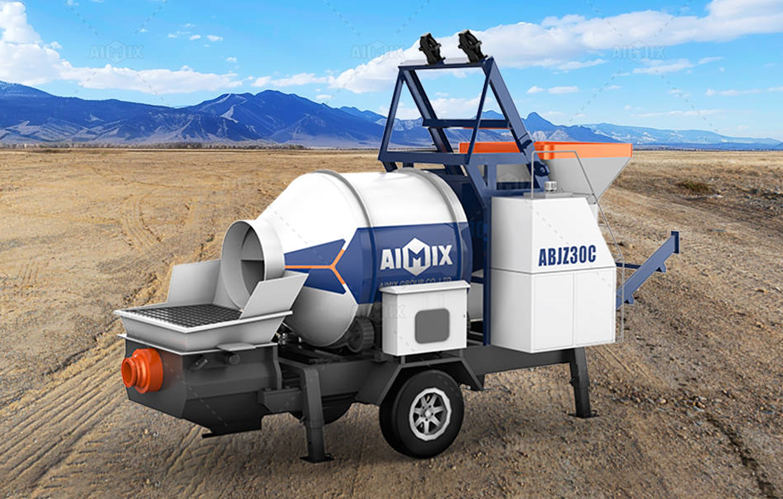